Suzanne Roberts Theatre
The Philadelphia Theatre Company’s dynamic Marquee signage
Completed in 2007, the Suzanne Roberts Theatre was designed by KieranTimberlake and features signage manufactured by Zahner.
Named for the former actress, playwright, and director, Suzanne Roberts Theatre is part of the initiative to enhance Philadelphia’s Avenue of the Arts. The building’s new marquee signage provides a striking statement about the quality of the arts program while maintaining the existing building and providing cover as an entrance soffit.

SUZANNE ROBERTS THEATRE IN PHILADELPHIA
PHOTO © A. ZAHNER COMPANY.

SUZANNE ROBERTS THEATRE IN PHILADELPHIA
PHOTO © A. ZAHNER COMPANY.

SUZANNE ROBERTS THEATRE IN PHILADELPHIA
PHOTO © A. ZAHNER COMPANY.
KieranTimberlake contracted Zahner to provide engineering and fabrication for the dynamic shape of the facade signage. Working through an intitial Design Assist phase, the project was developed for digital fabrication.
To produce the sculptural form, the marquee was engineered and fabricated using ZEPPS Technology, the Zahner system for building complex, curving sculptural forms. The technology enables fast installation, installed in just a few assemblies. Each assembly is made up of structural aluminum fins and ribs which are prefabricated in the Zahner facility offsite. These assemblies were then clad in a number of sheet metal skinned surfaces. KieranTimberlake worked with Zahner to select a iridescent stainless steel surface which provides the sign’s unique coloring.

DETAIL OF THE SUZANNE ROBERTS THEATRE IN PHILADELPHIA.
PHOTO © A. ZAHNER COMPANY.

CAD Diagrams showing individual Zahner assembly parts
Images © A. Zahner Company
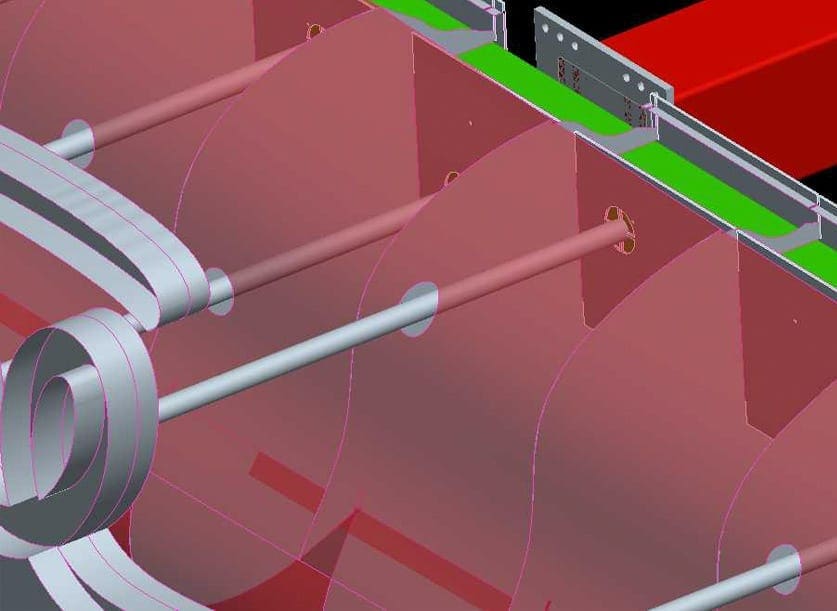


ZEPPS structure for Suzanne Roberts Theatre prior to cladding
Photo © A. Zahner Company
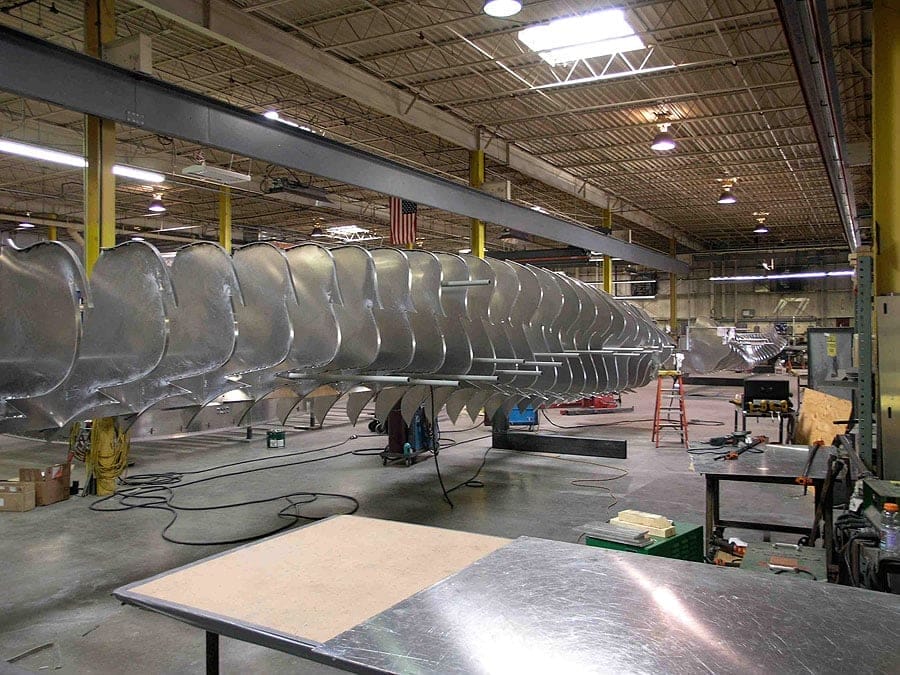
ZEPPS structure, clad in stainless steel skin with adhesive protective layer
Images © A. Zahner Company
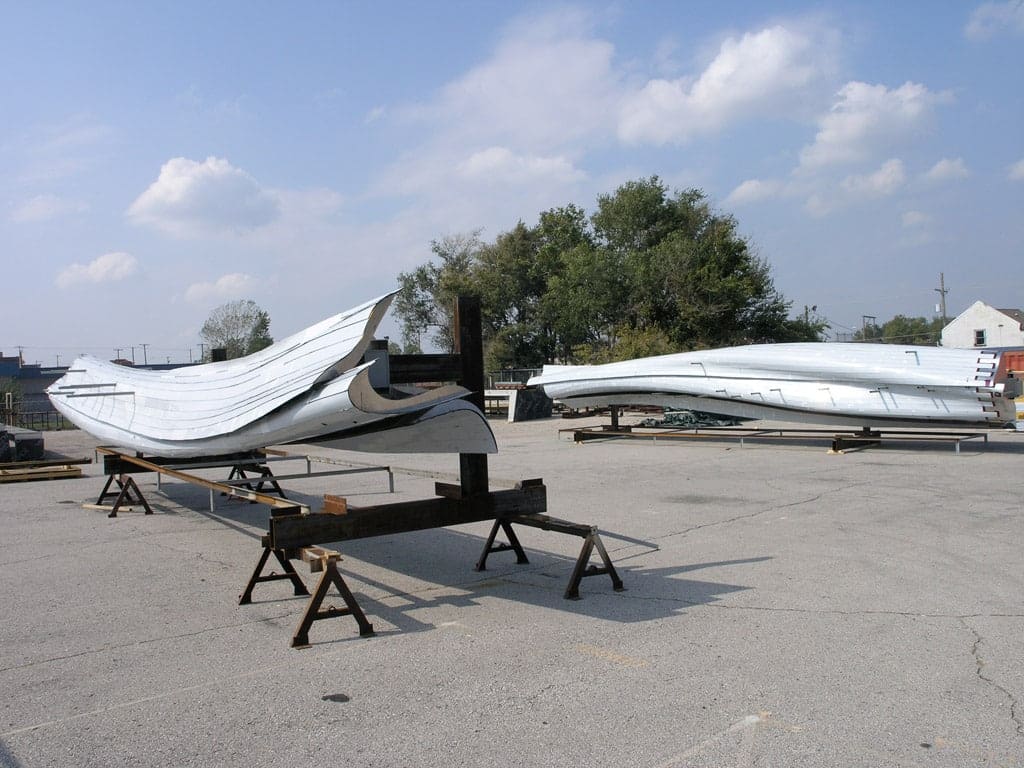
Two assemblies made using ZEPPS in the Zahner yard prior to shipment to Philadelphia
Photo © A. Zahner Company
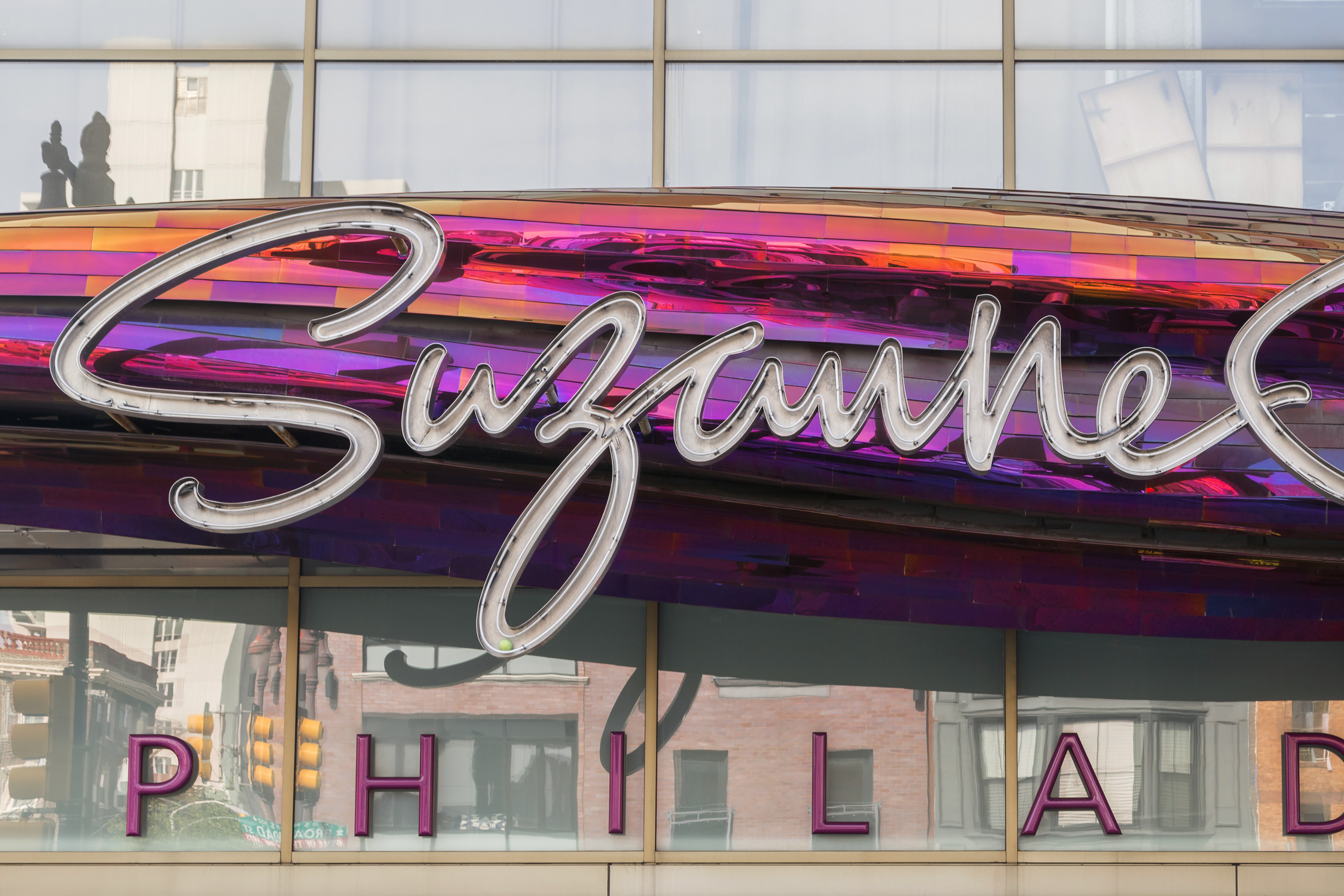
DETAIL OF THE SUZANNE ROBERTS THEATRE IN PHILADELPHIA.
Photo © A. Zahner Company