Guggenheim Hermitage Museum
The Guggenheim Hermitage Museum in Las Vegas
The Guggenheim Hermitage Museum was designed by Rem Koolhaus and Joshua Prince-Ramus of OMA as a center for Impressionist Art.
Zahner developed a preweathered patina on weathering steel for the gallery walls. The materials was used to create five-thousand square feet of wall space for the historic artworks. This preweathered steel material was used throughout the Guggenheim Hermitage Museum.
Today the weathering steel material is known as Solanum Steel, and uses a steel alloy which has replaced COR-Ten in popular usage. Many areas of the gallery were clad in this material, and served as a unique tone to back the acclaimed artworks of the nineteenth century.



Three of the walls clad in Zahner’s Solanum Steel were engineered to rotate, allowing curators to change the size and proportion of the four intermediary spaces within seconds. The wood floor and ceiling were produced using a finished maple surface.

Museum owners display a rotating wall.

A museum installer places a custom-magnet wall connection to hang a painting.
The Solanum Steel surface is a durable steel surface whose iron content enables magnetic properties. For this reason, the gallery opted for magnetic connections to the artworks, which meant that artworks could be easily installed and de-installed with minimal effort and clean-up. All of the paintings were hung from custom-made magnets, able to withstand several hundred pounds of vertical load.
The museum closed its doors in 2008 and was re-opened as an automobile museum. Zahner has since worked with OMA and REX (Ramus) on projects such as the Wyly Theatre in Dallas.

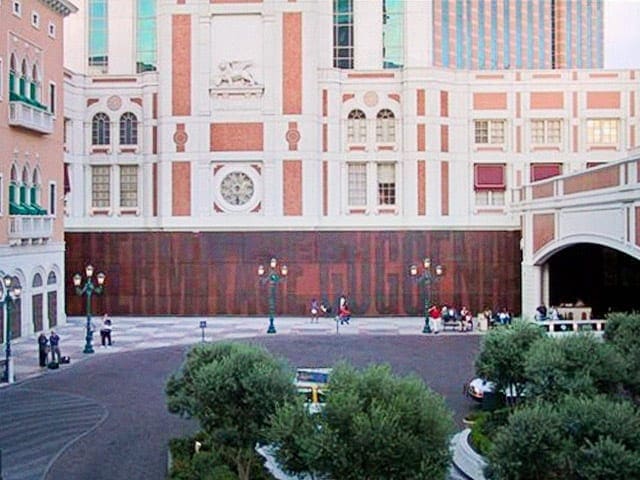